The new rule of supply chain design
Designing the optimal supply chain is fraught with complexity, but what if key variables were certain? Deterministic optimization offers a precise mathematical blueprint for network design, unlocking significant cost savings and efficiency.
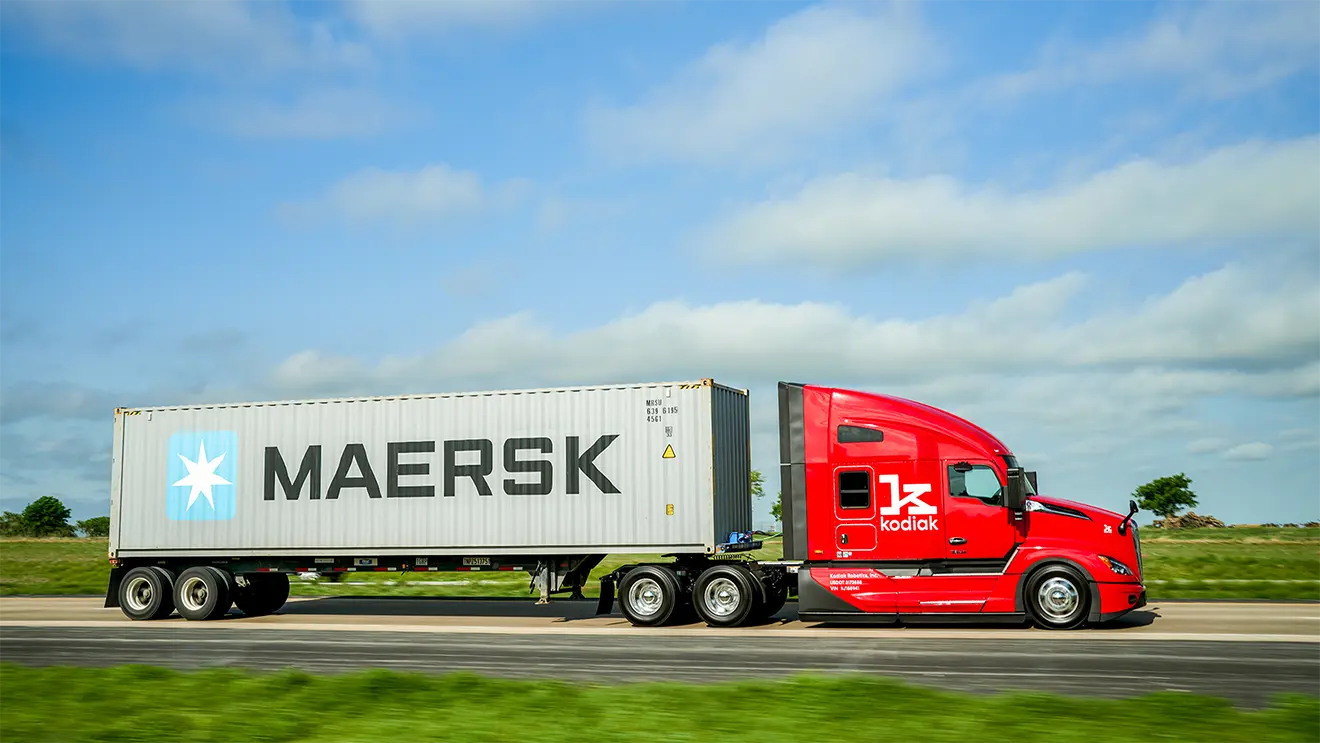
Supply chain management
is the backbone of modern business operations, ensuring that goods flow seamlessly from suppliers to customers. Strategic decisions in supply network design, facility location, and raw material selection play a crucial role in achieving efficiency and minimizing costs.
Under deterministic constraints—where demand, costs, and capacities are all known with certainty—these decisions become even more significant. However, the vast number of possible configurations leads to what is known as combinatorial explosion. This complexity can quickly surpass human decision-making abilities.
To address these challenges, optimization models based on mathematical programming offer a systematic approach. They help companies navigate complexity, reduce costs, improve service levels, and maintain competitiveness in the market.
This article explores the application of optimization models in supply network design, facility location, and raw material selection. It details their methodologies, discusses the benefits, and highlights real-world applications to demonstrate their value in today’s business environment.
1. Understanding Supply Chain Network Design
Supply chain network design involves strategically planning the structure of the supply chain. This includes suppliers, manufacturing facilities, warehouses, distribution centers, and customers. The main goal is to optimize the flow of goods, services, and information to meet customer demand efficiently while minimizing costs.
According to industry insights, this process requires building a detailed model that maps out logistics, such as facility locations and transportation routes. This ensures that products move through the supply chain cost-effectively and with minimal delays.
When operating under deterministic constraints, all parameters are fixed. This allows for precise optimization using mathematical models, leading to clear and actionable solutions. Continuous planning and refinement of the supply chain network are essential. These actions help maintain a streamlined and resilient supply chain, maximizing both profitability and customer satisfaction.
Key Factors in Network Design
Designing an optimal supply chain network requires considering multiple factors
- Cost: Includes transportation, warehousing, inventory, and labor costs, as well as capital investments for facilities and equipment. Cost-benefit analyses help minimize expenses while maintaining service quality.
- Demand Forecasting: Analyzing sales data, market trends, and external factors like seasonality ensures appropriate inventory levels, avoiding overstocking or shortages.
- Supplier Network: Building a reliable supplier network, ideally with proximity to facilities, reduces lead times and costs. Reliability and quality are critical, not just cost.
- Inventory Management: Optimizing ordering, storing, and restocking balances demand fulfillment with cost efficiency.
- Transportation and Logistics: Selecting the best transportation modes (e.g., road, rail, air, sea) and optimizing routes minimizes costs and ensures timely deliveries.
- Regulatory Compliance and Sustainability: Adhering to regulations and incorporating sustainable practices, such as eco-friendly sourcing, enhances brand reputation and avoids penalties.
- Technology and AI: Tools like IoT and AI improve forecasting, visibility, and decision-making, enhancing overall efficiency.
2. Optimization Models in Supply Chain Network Design
Optimization models are essential for managing the complexity of supply chain decisions. These models use mathematical programming to identify the optimal network configuration under deterministic conditions, where all inputs are known.
The most widely used model is Mixed Integer Linear Programming (MILP), which can handle complex supply chain problems by optimizing facility locations, transportation flows, and inventory levels while minimizing costs. According to a comprehensive review (ResearchGate, 2017), MILP was applied in 28 instances for forward supply chain network design (SCND).
Mixed Integer Non-Linear Programming (MINLP) is used when non-linear relationships, such as economies of scale, must be considered. This model was identified in three instances in the same review. Fuzzy Mixed Integer Programming (FMIP) introduces fuzzy logic to manage imprecise data and was used in four instances for forward SCND and three for closed-loop SCND. Stochastic Mixed Integer Programming (SMIP), although less common in deterministic settings, was noted in one instance for forward SCND.
Solution methods for these models include commercial solvers like IBM ILOG CPLEX (used in 16 forward SCND cases), as well as heuristics such as Genetic Algorithms (GA) and Particle Swarm Optimization (PSO), which are applied when exact solutions become computationally intensive. Additional techniques like Branch and Bound (B&B) and Lagrangian Relaxation (LR) are used to simplify particularly complex problems.
Software platforms such as anyLogistix support these optimization models, enabling network experiments to evaluate and select the most cost-effective supply chain configurations. For example, MILP can be used to determine the optimal number and location of distribution centers, minimizing both transportation and facility costs while ensuring demand is met.
Deterministic Constraints
In deterministic models, all parameters—such as demand, costs, and capacities—are assumed to be known with certainty. This simplifies the optimization process, allowing for precise solutions.
For instance, a Mixed-Integer Linear Programming (MILP) model might minimize the total cost, which typically includes both transportation costs and facility setup costs. The model operates under several key constraints
- Each customer must be served by exactly one facility.
- Total demand must be met without exceeding facility capacities.
- Fixed costs for opening facilities are included in the objective function.
These constraints ensure the model produces a feasible and optimal solution. As a result, the model might recommend selecting specific warehouse locations to serve a known set of customers, ensuring that all requirements are satisfied while minimizing total costs.
3. Facility Location Decisions
Facility location decisions are vital in supply chain network design. They determine the placement of manufacturing plants, warehouses, or distribution centers, directly impacting transportation costs, delivery times, and operational efficiency.
Several mathematical models address facility location problems. The p-Median Problem selects a fixed number (p) of facilities to minimize total weighted distance or cost to customers. This approach is ideal for optimizing service levels by reducing delivery distances.
The Uncapacitated Facility Location Problem (UFLP) introduces fixed facility costs, making the number of facilities a decision variable. This model balances facility setup costs against transportation expenses.
The Capacitated Facility Location Problem (CFLP) accounts for facility capacity limits, ensuring that no location is assigned more demand than it can handle.
Multi-Period Location Models plan for changes over time, such as fluctuating demand, by scheduling facility openings or closures across multiple periods.
Multi-Layer and Multi-Commodity Models address complex supply chain structures. They consider different facility types (e.g., plants, warehouses) and multiple products, integrating various supply chain layers.
These models are commonly solved using Mixed-Integer Linear Programming (MILP), with solvers like CPLEX optimizing the objective function while respecting capacity and demand constraints. A review of 115 articles revealed that 80% of facility location models focus on one or two layers, and 40% include multiple commodities, underscoring their prevalence in supply chain design.
Practical Application
Facility location models integrate with other supply chain decisions, such as transportation and inventory management. For example, a CFLP model might determine the optimal location for a new distribution center by minimizing the sum of fixed facility costs and variable transportation costs, ensuring all customer demand is met within capacity constraints. Tools like anyLogistix’s Greenfield Analysis can generate candidate locations and evaluate their cost-effectiveness.
4. Raw Material Selection
Raw material selection involves choosing suppliers and materials that meet quality standards while minimizing costs. This process is critical for ensuring product quality, reducing production costs, and maintaining supply chain efficiency. Optimization techniques and computational intelligence play a significant role
- Delphi Method: A structured approach to evaluate suppliers based on weighted criteria, such as economic environment (0.15), purchasing department functions (0.25), price stability (0.1), technical level (0.15), system management awareness (0.1), product qualification rate (0.1), quality inspection (0.1), and problem-solving timeliness (0.05). Suppliers are scored on a 5-point scale, and the highest-scoring supplier is selected.
- Trend-Adjusted Exponential Smoothing: Used to forecast raw material supply needs, achieving a forecast error rate within 9%. This method predicts monthly material requirements, reducing waste and optimizing inventory.
- Plato (Pareto) Principle: Identifies critical factors (80% impact) for raw material supply, such as price stability and product qualification rate, allowing businesses to focus on high-impact areas.
These methods ensure that raw material selection aligns with cost and quality objectives. For example, a study on school uniform supply chains used an optimization model based on the Internet of Things to minimize risks and costs by selecting optimal suppliers and material configurations.
Integration with Supply Chain
Raw material selection is often integrated into broader supply chain optimization models. For instance, a bi-objective MILP model can optimize supplier selection by maximizing profit and minimizing carbon emissions, considering material substitutions driven by price and environmental factors Emerald, 2018. Such models ensure that material choices support overall supply chain goals.
5. Benefits of Supply Chain Optimization
Through data-driven optimization, companies can achieve substantial cost reductions, boost operational efficiency, ensure quality and compliance, maximize profits, and enhance supply chain resilience.
Significant Cost Savings
Optimizing facility locations and transportation routes directly reduces delivery costs. For example, Coca-Cola HBC lowered transportation unit costs through logistics optimization. Accurate demand forecasting and effective inventory management help minimize overstocking and stockouts, cutting holding costs. Additionally, selecting cost-effective raw materials and suppliers lowers production expenses.
Increased Operational Efficiency
Strategic facility placement shortens transportation distances, speeding up order fulfillment. Optimized material selection also streamlines production processes, enabling faster formula determination. Efficient network designs help reduce bottlenecks, delays, and excess inventory, further boosting operational efficiency.
Ensured Quality and Compliance
Supplier selection methods such as the Delphi method ensure partners meet stringent quality standards, reducing defects and customer complaints. Incorporating compliance constraints in optimization models helps guarantee adherence to environmental and quality regulations, protecting against penalties.
Maximized Throughput and Profit
Optimization models prioritize high-value products and efficient production schedules to better meet market demand. Strategic facility locations also expand market coverage, increasing sales potential and overall profitability.
Enhanced Supply Chain Resilience
Scenario analysis, including digital twins, enables testing of multiple network configurations to ensure robust designs that can withstand disruptions like supplier interruptions. Integrating safety stock and contingency plans into optimization models further strengthens supply chain resilience.
Case Study: Coca-Cola HBC
Coca-Cola HBC, a leading beverage corporation, faced the challenge of managing complex product flows in the CIS region while aiming to reduce costs and uphold service standards. By leveraging anyLogistix software, the company developed a robust decision support system. This system enabled rapid testing of logistics and production hypotheses, providing optimal configurations and clear insights into vehicle requirements.
Through the implementation of cross-docking, Coca-Cola HBC was able to eliminate second-tier warehouses, significantly lowering facility costs. The optimized supply chain configurations also led to faster last-mile deliveries and reduced transportation unit costs. Additionally, safety stock levels were optimized, ensuring that service targets were consistently maintained without unnecessary inventory overhead.
The flexibility of the anyLogistix model allowed Coca-Cola HBC to easily adjust and test new supply chain configurations, supporting the company’s long-term adaptability. Overall, this optimization initiative demonstrated how advanced models can drive measurable improvements in cost, efficiency, and resilience, while aligning closely with Coca-Cola HBC’s strategic business objectives.